Unknown Facts About Alcast Company
Unknown Facts About Alcast Company
Blog Article
The Best Strategy To Use For Alcast Company
Table of ContentsSome Known Factual Statements About Alcast Company Get This Report on Alcast CompanyWhat Does Alcast Company Mean?Things about Alcast CompanyAlcast Company Things To Know Before You Get ThisThe Ultimate Guide To Alcast Company
The subtle difference hinges on the chemical web content. Chemical Comparison of Cast Aluminum Alloys Silicon advertises castability by minimizing the alloy's melting temperature level and boosting fluidness throughout casting. It plays a vital function in enabling detailed mold and mildews to be filled accurately. In addition, silicon adds to the alloy's toughness and put on resistance, making it important in applications where toughness is vital, such as auto components and engine parts.It additionally enhances the machinability of the alloy, making it simpler to refine right into completed products. In this way, iron contributes to the overall workability of light weight aluminum alloys. Copper boosts electrical conductivity, making it helpful in electric applications. It also improves rust resistance and contributes to the alloy's overall strength.
Manganese adds to the strength of aluminum alloys and enhances workability (Aluminum Casting). It is commonly made use of in wrought aluminum products like sheets, extrusions, and accounts. The existence of manganese help in the alloy's formability and resistance to splitting during construction processes. Magnesium is a lightweight component that gives toughness and impact resistance to light weight aluminum alloys.
The Best Strategy To Use For Alcast Company
Zinc enhances the castability of aluminum alloys and aids manage the solidification procedure throughout casting. It enhances the alloy's strength and firmness.
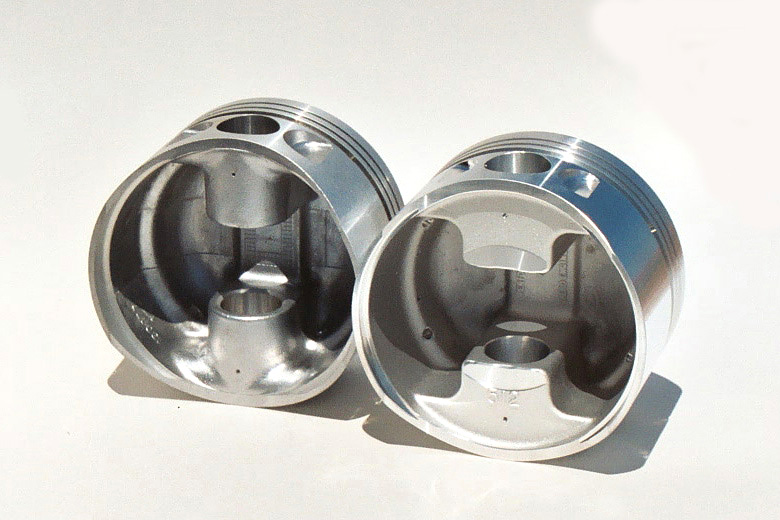
The key thermal conductivity, tensile stamina, return stamina, and prolongation differ. Select suitable raw materials according to the performance of the target product produced. Among the above alloys, A356 has the greatest thermal conductivity, and A380 and ADC12 have the cheapest. The tensile limit is the opposite. A360 has the very best yield stamina and the highest possible elongation rate.
The Greatest Guide To Alcast Company

In precision casting, 6063 is well-suited for applications where detailed geometries and premium surface finishes are critical. Instances consist of telecommunication units, where the alloy's exceptional formability permits smooth and visually pleasing styles while keeping structural stability. In the Illumination Solutions sector, precision-cast 6063 components develop sophisticated and reliable illumination view publisher site components that need elaborate forms and excellent thermal performance.
It leads to a better surface area finish and better corrosion resistance in A360. Moreover, the A360 shows exceptional elongation, making it suitable for facility and thin-walled parts. In accuracy spreading applications, A360 is fit for sectors such as Customer Electronic Devices, Telecommunication, and Power Devices. Its enhanced fluidity allows for intricate, high-precision elements like mobile phone housings and interaction gadget real estates.
Some Known Incorrect Statements About Alcast Company
Its distinct properties make A360 a valuable choice for precision spreading in these industries, improving item resilience and top quality. aluminum metal casting. Aluminum alloy 380, or A380, is a widely made use of casting alloy with a number of unique features.
In precision casting, light weight aluminum 413 radiates in the Customer Electronic Devices and Power Devices industries. This alloy's remarkable corrosion resistance makes it a superb selection for outdoor applications, making certain lasting, resilient products in the discussed sectors.
The Best Guide To Alcast Company
The aluminum alloy you choose will considerably impact both the spreading procedure and the properties of the final product. Due to the fact that of this, you should make your choice thoroughly and take an educated approach.
Establishing the most ideal aluminum alloy for your application will imply weighing a wide array of qualities. The initial category addresses alloy characteristics that influence the production process.
All about Alcast Company
The alloy you select for die casting directly impacts numerous facets of the spreading process, like how simple the alloy is to collaborate with and if it is prone to casting defects. Hot fracturing, likewise known as solidification cracking, is a normal die casting flaw for aluminum alloys that can result in interior or surface-level tears or fractures.
Certain light weight aluminum alloys are extra prone to warm cracking than others, and your choice needs to consider this. It can damage both the actors and the die, so you should look for alloys with high anti-soldering homes.
Deterioration resistance, which is already a noteworthy quality of light weight aluminum, can vary considerably from alloy to alloy and is a vital characteristic to consider depending on the ecological problems your product will be subjected to (aluminum casting manufacturer). Use resistance is another residential or commercial property typically looked for in light weight aluminum products and can distinguish some alloys
Report this page